Importance of understanding different types of aluminum welding techniques
Aluminum welding is a specialized skill that requires a deep understanding of various techniques. Understanding the different types of aluminum welding techniques is crucial to ensuring a successful and durable welding project. Each technique has its own set of advantages and limitations, and choosing the right one can significantly impact the quality and integrity of the weld.
One of the most commonly used aluminum welding techniques is Tungsten Inert Gas (TIG) welding. TIG welding provides superior control and precision, making it ideal for thin or delicate aluminum pieces. This technique uses a non-consumable tungsten electrode to create the weld, while an inert gas, such as argon, is used to shield the area from contamination. TIG welding produces clean and aesthetically pleasing welds with excellent strength and structural integrity. However, it requires a high level of skill and patience, as well as an understanding of the various techniques for manipulating the electrode and controlling the heat input.
Another popular aluminum welding technique is Metal Inert Gas (MIG) welding. MIG welding is faster and more versatile than TIG welding, making it suitable for thicker aluminum pieces and larger projects. This technique involves feeding a consumable wire electrode through a welding gun, which also supplies a shielding gas to protect the weld area from oxidation. MIG welding provides good penetration and reduced distortion, but it may result in lower weld quality compared to TIG welding. Understanding the proper wire feed speed, voltage, and gas flow is crucial for achieving strong and reliable MIG welds.
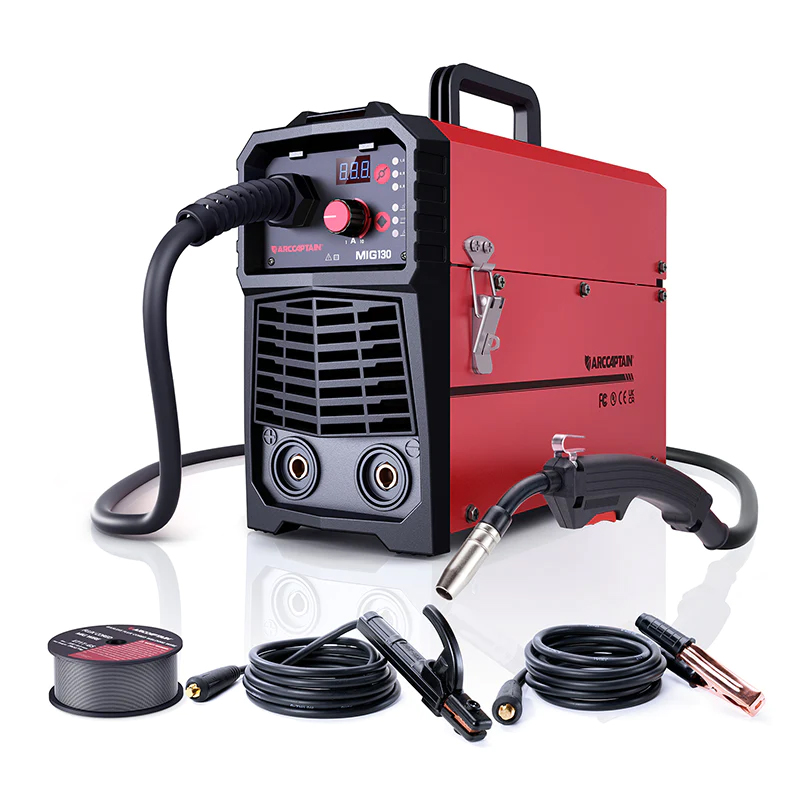
Additionally, there are other specialized aluminum welding techniques, such as Flux-Core Arc Welding (FCAW) and Gas Metal Arc Welding (GMAW). FCAW utilizes a flux-filled wire electrode that creates its own protective shield, eliminating the need for an external shielding gas. This technique is particularly useful in outdoor or windy conditions, where gas shielding may be challenging. GMAW, also known as MIG welding with pulsed current, allows for better control of heat input and reduces the risk of burn-through, making it suitable for thin aluminum sheets.
Understanding the different types of aluminum welding techniques is essential for ensuring the proper selection and execution of a welding project. Welders need to determine the thickness and type of aluminum being welded and consider the desired appearance and strength of the weld. By matching the right technique to the specific requirements of a welding job, welders can achieve high-quality, durable welds that meet industry standards and client expectations.
Ultimately, acquiring knowledge and expertise in aluminum welding techniques enables welders to expand their capabilities and tackle a wide range of projects. Whether it is TIG, MIG, FCAW, or GMAW, each technique has its own unique characteristics and advantages. By mastering different techniques, welders can confidently take on various welding applications and deliver exceptional results.
Types of Aluminum Welding
Aluminum welding is one of the most common and versatile methods used in various industries. Due to its lightweight and excellent corrosion resistance properties, aluminum is widely employed in the production of aircraft, automobiles, boats, and many other applications. However, welding aluminum can be quite challenging due to its low melting point and high thermal conductivity. To overcome these difficulties, several types of aluminum welding techniques have been developed. In this article passage, we will explore and discuss some of the most commonly used methods.
1. Gas Metal Arc Welding (GMAW):
Also known as MIG (Metal Inert Gas) welding, GMAW is a popular method for aluminum welding. It uses a consumable electrode wire, which is fed through a handheld welding gun. The electrode wire is heated and melted along with the base material by an electric arc. Simultaneously, a shielding gas, such as argon or a mixture of argon and helium, is used to protect the weld from atmospheric contamination. GMAW is relatively easy to learn and provides a high deposition rate, making it suitable for welding thicker aluminum materials.
2. Tungsten Inert Gas Welding (TIG):
TIG welding, also known as Gas Tungsten Arc Welding (GTAW), is widely used for aluminum welding due to its versatility and ability to produce high-quality welds. In this method, a non-consumable tungsten electrode creates the electric arc, while a separate filler wire is manually added to the weld joint. Argon gas is used as a shielding gas to protect the weld zone. TIG welding allows precise control over the heat input, making it ideal for welding thin aluminum sheets and creating aesthetically pleasing welds.
3. Flux-Cored Arc Welding (FCAW):
FCAW is another commonly used aluminum welding method, especially in outdoor or windy environments. Similar to GMAW, it uses a continuously fed electrode wire. However, unlike GMAW, FCAW uses a tubular electrode filled with flux. This flux creates a shielding gas and also releases additional components during the welding process, improving the quality and mechanical properties of the weld. FCAW is known for its high deposition rate and deep penetration, making it suitable for thicker aluminum sections.
4. Pulse Arc Welding:
Pulse arc welding is a more advanced technique that provides greater control over heat input and minimizes distortion. It is particularly useful when welding thin aluminum sections or when welding dissimilar materials. The pulse arc produces a series of repetitive high-frequency current pulses, allowing for precise control over the weld pool. This method reduces the chances of burn-through or excessive heat-affected zones.
These are just a few of the many aluminum welding techniques available. Each method has its advantages and suitability based on the requirements of the project, the type and thickness of the aluminum being welded, and the desired quality of the weld. While aluminum welding can be challenging, with the right technique, equipment, and training, it can be accomplished successfully, resulting in strong and high-quality welds.
Gas Metal Arc Welding (GMAW)
Gas Metal Arc Welding (GMAW) is a widely used welding process that plays a crucial role in various industries. It is also known as Metal Inert Gas (MIG) welding, as it employs a shielding gas to protect the weld pool from atmospheric contamination. GMAW is preferred for its versatility, speed, and ease of use, making it suitable for both professional welders and beginners.
The process of GMAW involves creating an electrical arc between a consumable electrode and the base metal. The electrode, or the wire, is continuously fed through a welding gun, which also releases the shielding gas that protects the weld area. This gas is usually a mixture of argon, carbon dioxide, or a combination of both.
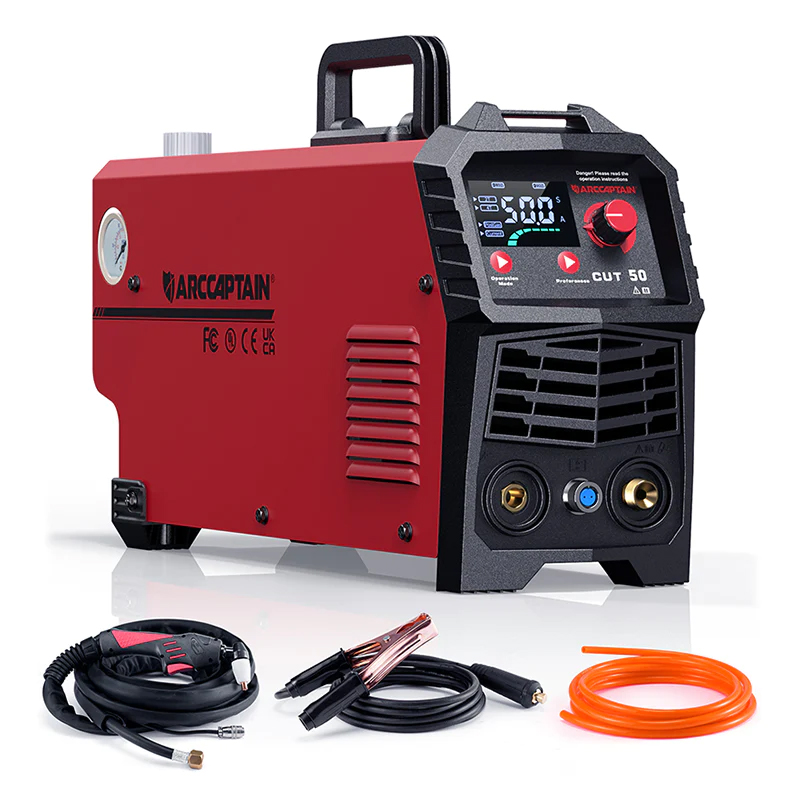
One of the main advantages of GMAW is its ability to weld various metals, including steel, aluminum, stainless steel, and nickel alloys. This versatility makes it a popular choice for industries such as automotive, construction, aerospace, and manufacturing. Additionally, GMAW is widely used in repair and maintenance jobs due to its ability to join dissimilar metals.
Another benefit of GMAW is its high welding speed. Since the wire is continuously fed, the process is efficient and can be automated, enhancing productivity and reducing labor costs. Furthermore, GMAW provides excellent control over the welding parameters, allowing welders to achieve precise and consistent welds.
GMAW also offers better weld quality compared to other welding processes. The shielding gas forms a protective barrier around the weld pool, preventing the formation of defects such as porosity and oxidation. This results in strong, reliable welds with improved mechanical properties.
One of the drawbacks of GMAW is its reliance on a consistent supply of shielding gas. Any disruption or absence of gas can lead to reduced weld quality. Additionally, GMAW requires a clean and properly prepared work surface to ensure optimal performance. Any impurities or contaminants on the metal surface can negatively impact the weld integrity.
Overall, Gas Metal Arc Welding (GMAW) is a highly efficient and versatile welding process. Its ability to weld a wide range of metals with excellent control and speed makes it a popular choice in various industries. Though it requires careful attention to shielding gas and surface preparation, the benefits of GMAW in terms of weld quality and productivity make it an invaluable technique for both professionals and hobbyists alike.
Description of GMAW
Gas Metal Arc Welding (GMAW), also known as Metal Inert Gas (MIG) welding, is a widely used welding process in various industries. It is a semi-automatic process that uses an electric arc formed between a consumable wire electrode and the workpiece while shielding the arc with an externally supplied gas.
GMAW offers several advantages over other welding processes, making it a popular choice among welders. One key benefit is its versatility. GMAW can be used to weld a wide range of materials, including carbon steel, stainless steel, and aluminum. This makes it suitable for a variety of applications, from automotive and aerospace manufacturing to sheet metal fabrication.
The GMAW process is relatively straightforward. The welding machine supplies a constant current to the electrode, which is continuously fed into the weld joint at a controlled speed. As the wire electrode melts, it creates a molten pool that fuses the workpieces together, forming a strong and durable weld. The heat generated from the electric arc also helps to ensure proper fusion between the base metal and the filler material.
A shielding gas is required in GMAW to protect the molten metal from atmospheric contamination. The choice of shielding gas depends on the type of materials being welded and the desired characteristics of the weld. Argon, carbon dioxide, or a mixture of both are commonly used gases in GMAW. Argon provides excellent arc stability and produces a clean weld, while carbon dioxide offers better penetration and higher welding speeds.
Another advantage of GMAW is its high welding speed. The continuous feeding of the wire electrode allows for a faster deposition rate, reducing the overall welding time. This makes GMAW a preferred choice for applications that require high productivity, such as mass production and assembly line welding.
Furthermore, GMAW offers excellent control over the welding process. Welders can adjust the welding current, voltage, and wire feed speed to achieve the desired weld profile and quality. This level of control allows for precise and consistent welds, resulting in superior joint strength and appearance.
Despite its numerous advantages, GMAW also has a few limitations. It is not suitable for welding thick materials, as the heat input may cause excessive distortion or warping. Additionally, the process requires a clean and well-prepared surface for optimal results. Any impurities or contaminants on the workpiece can affect the quality of the weld.
In conclusion, Gas Metal Arc Welding (GMAW) is a versatile, efficient, and widely used welding process. It offers excellent control, high welding speeds, and the ability to weld a wide range of materials. Whether in manufacturing, construction, or automotive industries, GMAW continues to play a vital role in creating strong and reliable welds.
Advantages and disadvantages of GMAW
Gas Metal Arc Welding (GMAW), also known as Metal Inert Gas (MIG) welding, is a popular welding process in various industries. It involves using a continuous wire electrode and a shielding gas to generate the welding arc. GMAW offers several advantages, but it also carries a few disadvantages that need to be considered.
One of the most significant advantages of GMAW is its versatility. It can be used to weld a wide range of materials, including carbon steel, stainless steel, and aluminum. This makes it a preferred choice for manufacturers as it allows them to work with different components and produce diverse products. The process is relatively fast and efficient, enabling welders to complete large projects within a shorter timeframe compared to other welding methods. Additionally, GMAW ensures better control over the welding process, resulting in high-quality welds with minimal defects.
Another advantage of GMAW is its ease of use. The equipment and setup required for GMAW are relatively simple, making it accessible to welders of varying skill levels. This means that companies can employ welders with little experience and train them quickly to become proficient in GMAW. Additionally, GMAW offers excellent arc visibility due to the use of a shielding gas and a solid wire electrode, allowing welders to have a clear view of the welding area and achieve greater precision.
However, GMAW also has its disadvantages. One of the main drawbacks is the high cost of equipment and consumables. Compared to other welding processes, GMAW requires specialized equipment and shielding gases, which can significantly increase the initial setup costs. The continuous wire electrode used in GMAW also needs to be regularly replaced, resulting in ongoing expenses. Moreover, GMAW is not suitable for outdoor applications or in areas with high wind, as the shielding gas can be easily blown away, leading to improper shielding and poor weld quality.
Another disadvantage of GMAW is the need for a clean working environment. As this welding process uses a shielding gas to protect the weld pool, any contamination, such as dirt, rust, or grease, on the workpiece or in the surrounding area can result in poor weld quality. Therefore, proper cleaning and preparation of the workpiece are essential for successful GMAW.
In conclusion, GMAW offers numerous advantages, including versatility, speed, and ease of use, making it a widely used welding process in various industries. Nonetheless, its high initial and ongoing costs, along with the requirement for a clean working environment, are some of the disadvantages that need to be considered. By weighing these pros and cons, welders and manufacturers can make informed decisions on whether GMAW is the most suitable welding process for their specific applications.
Gas Tungsten Arc Welding (GTAW)
Gas Tungsten Arc Welding (GTAW) is a widely used welding process that offers exceptional precision and high-quality results. Also known as Tungsten Inert Gas (TIG) welding, GTAW utilizes a non-consumable tungsten electrode to create an arc between the electrode and the metal being welded.
GTAW involves the use of a shielding gas, typically argon or helium, to protect the weld area from atmospheric contamination. This shielding gas also helps maintain a stable arc and prevents oxidation or other undesirable effects on the weld metal.
One of GTAW’s main advantages is its versatility in welding a variety of materials, including carbon steel, stainless steel, aluminum, nickel alloys, and even exotic metals like titanium. The process is commonly employed in industries such as aerospace, automotive, and construction, where the superior quality and strength of the welds are paramount.
One of GTAW’s key features is its ability to produce exceptionally clean and precise welds. This is due to the non-consumable tungsten electrode, which allows for finer control of the arc compared to other welding methods. Welders can easily manipulate the arc length, heat input, and travel speed, resulting in precise bead profiles and minimal distortion on the workpiece.
Moreover, GTAW offers excellent aesthetic results, making it particularly suitable for applications where the appearance of welds is crucial, such as in architectural designs or artwork. The welds produced by GTAW typically have a smooth and shiny finish, requiring minimal post-weld finishing processes.
However, GTAW does require considerable skill and patience to master. The process demands steady hands and good hand-eye coordination to accurately control the movement of the torch and maintain the ideal arc length. Additionally, it is crucial to properly prepare the base materials to ensure clean and contaminant-free welds.
Furthermore, GTAW is generally slower than other welding techniques due to its precise nature. This can make it less suitable for large-scale production, where speed and efficiency are primary concerns. However, the superior quality of GTAW welds compensates for the additional time required for the operation.
In conclusion, Gas Tungsten Arc Welding (GTAW) or Tungsten Inert Gas (TIG) welding is a widely utilized welding process known for its precision, versatility, and high-quality results. Its ability to produce clean and aesthetically pleasing welds, coupled with its suitability for a wide range of materials, makes it a preferred choice in various industries. While GTAW demands skill and patience, the superior quality of its welds and the ability to achieve precise bead profiles make it a valuable technique in welding applications.
Description of GTAW
GTAW, also known as Gas Tungsten Arc Welding or TIG (Tungsten Inert Gas) welding, is a widely used welding process that offers high-quality and precise welds. It is often preferred for its ability to produce clean and aesthetically pleasing welds with minimal spatter.
This welding technique utilizes a non-consumable tungsten electrode to create the arc and heat required for the melting and joining of metals. The filler material, if necessary, is added separately. An inert gas, such as argon or helium, helps to shield the welding area from atmospheric contamination. This gas also acts as a coolant, preventing the electrode and the workpiece from overheating.
One of GTAW’s key features is its versatility. It can be used to weld a wide range of metals, including stainless steel, aluminum, copper, and titanium. It offers excellent control over the welding process, allowing welders to work with thin materials as well as thicker sections.
GTAW is especially favored in industries where precision and aesthetic appeal are of utmost importance, such as the automotive, aerospace, and jewelry sectors. Its ability to create intricate and detailed welds makes it suitable for applications where welding appearance matters, like sculpture or artwork fabrication.
Due to its complexity, the GTAW process requires a high level of skill and craftsmanship, but the results are worth the effort. Welders must carefully regulate the heat input and maintain a stable arc length to ensure optimal weld quality. This level of control allows the operator to manipulate the welding parameters according to the project’s specific requirements.
Another advantage of GTAW is its ability to produce deep-penetration welds. This is achieved by adjusting the welding parameters, such as the current and the electrode angle. The process also creates a narrow fusion zone, reducing the risk of distortion and preserving the mechanical properties of the base material.
However, GTAW does have its limitations. It is a slower welding process compared to some other techniques, which can result in increased production time and cost. Additionally, it is not suitable for all joint configurations, particularly those involving large gaps or mismatches.
In summary, GTAW is a versatile and precise welding process used in various industries. Its ability to create clean and aesthetically pleasing welds, as well as its compatibility with a wide range of metals, makes it a popular choice for applications that require high-quality welds. While it does require a high level of skill and may have some limitations, the superior results achieved with GTAW justify its use for many welding projects.
Advantages and disadvantages of GTAW
GTAW, or Gas Tungsten Arc Welding, is a widely used welding technique that offers several advantages and disadvantages. Also known as TIG (Tungsten Inert Gas) welding, GTAW is a precise and high-quality welding method that utilizes a non-consumable tungsten electrode along with an inert gas to protect the weld area from atmospheric contamination.
One of the major advantages of GTAW is its versatility. This welding process can be used with a wide range of metals, including steel, stainless steel, aluminum, nickel alloys, copper, and more. This makes it a popular choice for various industries such as automotive, aerospace, and construction, where different materials may need to be joined together.
Another significant advantage of GTAW is the superior quality of the weld produced. This welding technique allows for precise control of the heat input, resulting in clean and aesthetically pleasing welds. The weld bead is usually smooth and free from spatter, ensuring a strong and long-lasting bond between the metals. Additionally, the absence of flux in GTAW reduces the chances of weld contamination, making it particularly suitable for applications where cleanliness is crucial, such as in the food and pharmaceutical industries.
GTAW also offers excellent control over the welding process, thanks to its non-consumable tungsten electrode. The welder can adjust the heat input, welding speed, and arc length, allowing for precise control over the welding parameters. This makes it easier to achieve accurate and consistent welds, even on thin materials. Furthermore, GTAW can be performed in all positions, including overhead and vertical, making it versatile for welders working in various positions.
However, despite its many advantages, GTAW has certain limitations and disadvantages. One of the main drawbacks is the relatively slow welding speed compared to other welding methods such as MIG (Metal Inert Gas) or Stick welding. This reduced productivity can be a significant downside when working on large projects or in situations where speed is crucial. Additionally, GTAW requires a skilled operator who has received proper training to ensure the correct technique and parameter settings are used.
Another disadvantage of GTAW is the complexity of the equipment required. Compared to other welding techniques, GTAW setups are generally more expensive and sophisticated. The need for a constant supply of inert gas, such as argon, and the requirement for a specialized power source adds to the overall cost of GTAW. Furthermore, the setup and preparation time for GTAW can be longer, making it less suitable for applications where time efficiency is essential.
In conclusion, GTAW offers several significant advantages, including versatility, excellent weld quality, and precise control. However, the limitations of slower welding speed, higher equipment costs, and increased complexity need to be taken into consideration when deciding on the appropriate welding technique for a particular project. Welders and industries should carefully weigh the advantages and disadvantages of GTAW before choosing whether to utilize this method for their welding needs.
Laser Beam Welding (LBW)
Laser Beam Welding (LBW) is a highly advanced technique that has revolutionized the welding industry. It offers several advantages over traditional welding methods, making it a preferred choice for numerous applications.
LBW utilizes a high-intensity laser beam to melt and bond materials together. The laser beam is focused on the welding area, producing a concentrated heat source that creates a narrow and deep weld. This precise and controlled process ensures high strength and accuracy in the final weld.
One of the key benefits of LBW is its ability to weld materials with a high melting point, such as stainless steel and titanium. Unlike conventional welding techniques, LBW does not rely on external heat sources that may require intense temperatures to melt these materials. This prevents any potential damage to the surrounding areas and reduces the risk of distortion in the final product.
Another advantage of LBW is its minimal heat-affected zone (HAZ). The HAZ is the area surrounding the weld where the material’s properties may be altered due to excessive heat exposure. With LBW, the laser beam quickly heats up and cools down the material, resulting in a significantly smaller HAZ compared to other methods. This is particularly beneficial when working with heat-sensitive materials or components that require precise control and minimal distortion.
Additionally, LBW offers exceptional weld quality, including strong metallurgical bonding and reduced porosity. The laser beam’s concentrated heat source enables deep penetration into the material, effectively creating a robust and sound weld. The absence of filler materials in LBW further enhances the overall weld quality by eliminating potential defects and ensuring a clean and tidy joint.
Notably, LBW also provides increased productivity and efficiency. The process is fully automated and highly programmable, allowing for quick and precise welding operations and minimizing production time and costs. Moreover, the contact-free nature of LBW eliminates the need for clamping or fixturing, further streamlining the production process and reducing material handling requirements.
LBW finds extensive applications in various industries, including automotive, aerospace, electronics, and medical. Its ability to join dissimilar materials, such as steel and aluminum, has opened up new possibilities for lightweight and high-performance designs. Moreover, LBW’s precise nature makes it suitable for intricate and complex assemblies, where accuracy and precision are paramount.
In conclusion, Laser Beam Welding (LBW) has emerged as a cutting-edge technology in the welding industry due to its numerous advantages. From its ability to weld high-melting-point materials to its minimal heat-affected zone, LBW offers unmatched quality, productivity, and versatility. As industries continue to demand efficiency and precision, LBW stands at the forefront, shaping the future of welding.
Description of LBW
One of the most debated and complicated rules in cricket is LBW, which stands for Leg Before Wicket. LBW is a crucial decision that can greatly impact the outcome of a match. This rule essentially means that if the bowler delivers a ball that would have hit the stumps but is intercepted by the batsman’s leg instead, the batsman can be given out if certain conditions are met.
To understand the LBW rule better, it is essential to know about the three main criteria that the umpire considers when making this decision. First and foremost, the point of impact on the batsman’s leg has to be in line with the stumps. If the contact is outside the line, regardless of its angle, the batsman cannot be given out.
Secondly, the ball has to hit the batsman in line with the stumps after pitching. If the ball pitches outside the leg stump, the batsman is exempt from dismissal. Additionally, if the ball pitches outside the off stump and then proceeds to hit the batsman in line with the stumps, it can still be considered an LBW dismissal if the umpire deems the batsman to have made no attempt to play a shot.
Lastly, the umpire considers whether the batsman was offering a shot at the delivery. If the batsman attempts to play the ball with either the bat or the pad and makes contact with the ball, he cannot be given out LBW. However, if the umpire believes that the batsman made no genuine attempt to play the ball, he can rule the batsman out.
The LBW rule can be a source of controversy due to its subjective nature. In some instances, the umpire may have to rely on technology, such as ball-tracking systems, to make an accurate decision. The use of technology has brought greater precision to the game but has also sparked debates regarding the validity of the decision-making process.
LBW decisions can significantly impact a match’s momentum. A dismissal can turn the tide in favor of the bowling side, giving them greater control over the game, while a wrong decision can cause frustration and disappointment for the batting side. For this reason, LBWs are often referred to as the third umpire for review, especially in high-stakes matches.
Overall, the LBW rule is an integral part of cricket, adding an element of excitement and tension. It requires the umpire to make accurate decisions, often under immense pressure, using skill and judgment. While it may be a contentious rule, it undoubtedly adds to the thrill of the sport and tests the skills of both batsmen and bowlers.
Advantages and disadvantages of LBW
The decision review system (DRS) or the third umpire referral system has significantly improved the accuracy of LBW decisions in cricket matches. While the LBW (leg before wicket) decision has always been a hotly debated topic among players, experts, and cricket enthusiasts, the introduction of technology has brought certain advantages and disadvantages to the game.
One of the main advantages of the LBW decision being reviewed by technology is the increased accuracy in decision-making. Previously, the on-field umpires were solely responsible for determining whether the ball would have hit the stumps if not for the batsman’s leg obstructing its path. This was often a difficult judgment call as the umpires were positioned far away from the action. The DRS allows for multiple camera angles, slow-motion replays, and ball-tracking technology, which provides a more comprehensive view of the situation. As a result, the decision-making process is fairer, reducing the chances of an inaccurate lbw decision.
Another advantage of the DRS is the opportunity it provides for the players to challenge a decision they feel is incorrect. This introduces an element of strategy to the game as each team is allowed a limited number of unsuccessful reviews per innings. It encourages the players to stay alert and make wise decisions about when to use their review, adding an exciting tactical aspect to the game.
However, there are also disadvantages to the LBW decision being reviewed by technology. One of the main criticisms is the potential disruption of the game’s flow. The decision-making process can take a considerable amount of time, with players and spectators left waiting for the technology to deliver its verdict. This can often break the momentum of the game and reduce its excitement and intensity.
Additionally, there have been instances when the DRS has been criticized for being inconsistent in its decision-making. While technology provides a more accurate view of the LBW situation, there have been occasions when even replays and ball-tracking technology have failed to conclusively determine whether the ball would have hit the stumps. This can lead to frustration among players and fans alike when a seemingly clear-cut lbw decision remains unresolved.
In conclusion, the use of technology in reviewing LBW decisions has its advantages and disadvantages. It significantly improves the accuracy of decision-making and adds a tactical element to the game. However, it can also disrupt the flow of the game and has faced criticism for inconsistency. Ultimately, the decision to utilize technology in cricket rests on striking a balance between maintaining the integrity of the game and preserving its traditional aspects.
Resistance Spot Welding (RSW)
Resistance spot welding (RSW) is a widely used joining technique in the field of manufacturing. It allows two or more metal sheets to be securely connected by applying heat and pressure at specific points. This process is highly efficient and cost-effective, making it a preferred method for numerous industries.
The principle behind resistance spot welding lies in the creation of an electrical circuit. By passing an electrical current through the metal sheets, a significant amount of heat is generated at the contact points. The heat softens the metals, and when sufficient pressure is applied, they fuse together, forming a strong bond.
One of the main advantages of resistance spot welding is its speed. The process can be completed within milliseconds, making it ideal for high-volume production lines. Additionally, RSW is highly automated, ensuring consistent and reliable results. It eliminates the need for additional materials such as adhesives or fasteners, further simplifying the assembly process.
Another advantage of RSW is its versatility. It can join a wide range of metals, including steel, aluminum, and copper. This flexibility contributes to its widespread usage in industries such as automotive manufacturing, aerospace, and electrical appliance production. Whether it is joining panels in a car body or connecting electrical wires, resistance spot welding proves to be an effective solution.
Furthermore, resistance spot welding offers excellent joint strength. The heat generated during the process causes the metal to melt, allowing it to merge together. This results in a seam that exhibits superior mechanical properties, including high tensile strength and resistance to fatigue. These qualities are crucial for ensuring the longevity and safety of the final product.
Although resistance spot welding has its advantages, there are a few limitations to consider. Since the process relies on the electrical conductivity of the metals being joined, it may not be suitable for materials with low conductivity, such as some types of stainless steel. Additionally, the thickness of the materials may limit the feasibility of using RSW. Very thin or thick sheets may require alternative welding methods.
In conclusion, resistance spot welding is a highly effective and widely used technique for joining metal sheets. Its speed, versatility, and excellent joint strength make it a preferred choice for various industries. Despite some limitations, RSW continues to play a crucial role in manufacturing, enabling the production of durable and reliable products.
Description of RSW
RSW, also known as Robert Swartwood, is a renowned American author known for his gripping storytelling and ability to keep readers on the edge of their seats. With numerous accolades and a loyal fan base, RSW has solidified his place in the world of literature.
One of the defining characteristics of RSW’s writing is his mastery of suspense and thrill. His novels are filled with unexpected twists and turns, keeping readers guessing until the very end. RSW has a knack for creating complex and flawed characters, making them relatable and intriguing to readers. His ability to balance the psychological aspects of his characters with fast-paced action is truly commendable.
Another aspect that sets RSW apart from other authors is his unique writing style. His prose is concise and effective, allowing readers to easily immerse themselves in the story. RSW’s writing is marked by his attention to detail, painting vivid pictures in the minds of his readers. His descriptive language creates a palpable atmosphere, making it easy for readers to become engaged in the story.
Furthermore, RSW’s diverse range of genres is another reason for its popularity. From thriller and suspense to horror and science fiction, he has proven his versatility as an author. Each novel exhibits his ability to seamlessly transition between genres, leaving readers excited for what he will write next.
RSW’s novels are known for their unpredictable plots and unexpected endings. With each turn of the page, readers are constantly surprised and captivated by the story. RSW has a skill for keeping readers engaged from start to finish, creating an addictive reading experience.
Ultimately, RSW’s writing is a testament to his talent and dedication to the craft of storytelling. With his gripping plots, well-developed characters, and impeccable writing style, he has undoubtedly left his mark on the literary world. As readers eagerly await his next work, one thing is for certain – RSW will continue to enchant and thrill his audience for years to come.
Advantages and disadvantages of RSW
RSW, or Resistance Spot Welding, is a common method used in the manufacturing industry to join two or more metal pieces together. This welding technique offers several advantages and disadvantages that should be considered before its application.
One of the significant advantages of RSW is its high production speed. With the ability to perform multiple welds simultaneously, RSW allows for quick assembly of metal components, making it an ideal choice for mass production. This increased efficiency ultimately leads to cost savings in labor and time.
Additionally, RSW offers excellent weld quality and strength. The welds created through spot welding are known to have high integrity. The process ensures a strong bond between the metals, providing structural strength and durability. This makes RSW suitable for applications that require reliable joints, such as automotive manufacturing and construction.
Furthermore, RSW eliminates the need for additional materials. Unlike other welding techniques that require filler metals or fluxes, spot welding utilizes the metals being joined without any added components. This not only simplifies the welding process but also minimizes material costs, making it an economical choice.
However, along with the advantages, there are also some disadvantages to consider when using RSW. One of the main drawbacks is the limited joint thickness. RSW is most effective for thin sheets of metal, generally ranging from 0.5mm to 3mm. If thicker pieces need to be joined, alternative welding methods, such as TIG or MIG welding, might be more appropriate.
Another disadvantage of RSW is the need for clean and properly prepared surfaces. The welding electrodes must be in direct contact with the metals being joined to ensure a successful weld. Any contaminants or oxidation on the surfaces can hinder this contact, leading to weak or faulty welds. Therefore, proper surface preparation becomes crucial, adding an extra step to the welding process.
Moreover, RSW requires access to both sides of the metals being joined. As the name suggests, spot welding involves concentrating the welding heat and pressure in a specific area. This requires accessibility to both the front and back sides of the metal pieces. In situations where the backside is inaccessible, alternative welding techniques may need to be employed.
In conclusion, RSW offers several advantages, including high production speed, excellent weld quality, and cost-effectiveness. However, it has limitations in terms of the joint thickness it can accommodate and the need for clean surfaces and accessibility from both sides. Considering these factors is essential to determine if RSW is the appropriate welding method for a particular application.